sustainability
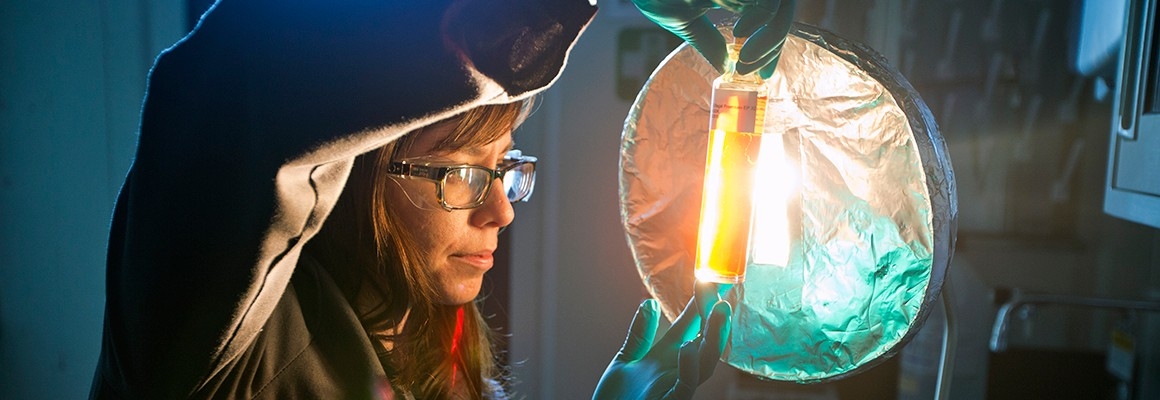
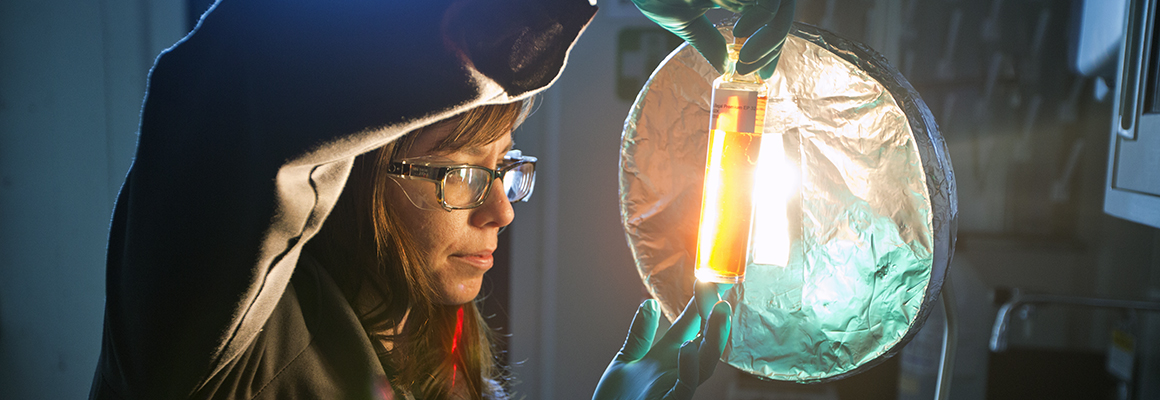
For over 140 years, Chevron has continued to evolve and help meet the energy demand of a growing world. Chevron aims to grow its oil and gas business, lower the carbon intensity of its operations and pursue new lower carbon businesses in renewable fuels, carbon capture and offsets, hydrogen, and other emerging technologies. Chevron’s approach to sustainability is integrated throughout its business. Chevron strives to protect the environment, empower people and get results the right way.
chevron oronite's lower carbon activities and opportunities


Chevron believes the future of energy is lower carbon. That’s why Chevron is focused on lowering the carbon intensity of its operations and investing in lower carbon technologies. Likewise, lower carbon plays an important role in Chevron Oronite’s strategy. We aim to lower the carbon intensity of our operations and products and help enable lower carbon solutions for end use applications.
Click below to learn more about the work we’re doing at different stages of the product lifecycle.