PARATONE® viscosity modifiers
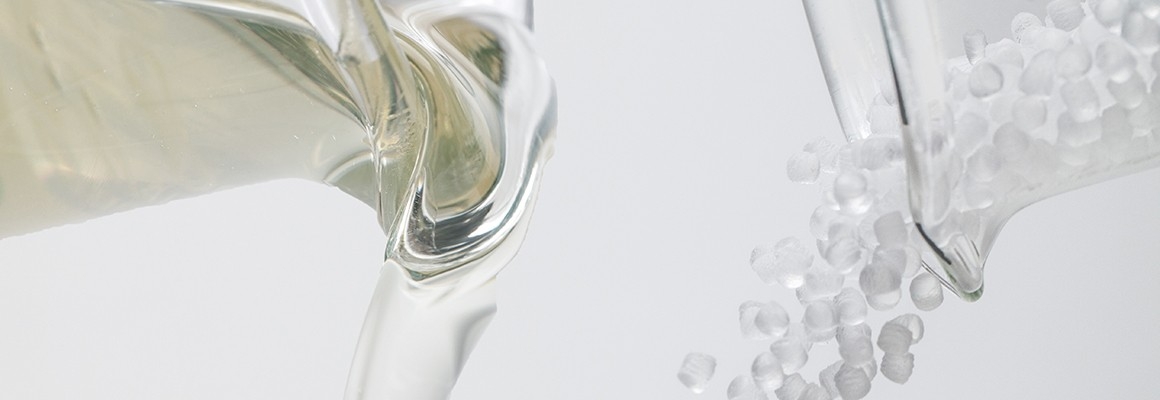
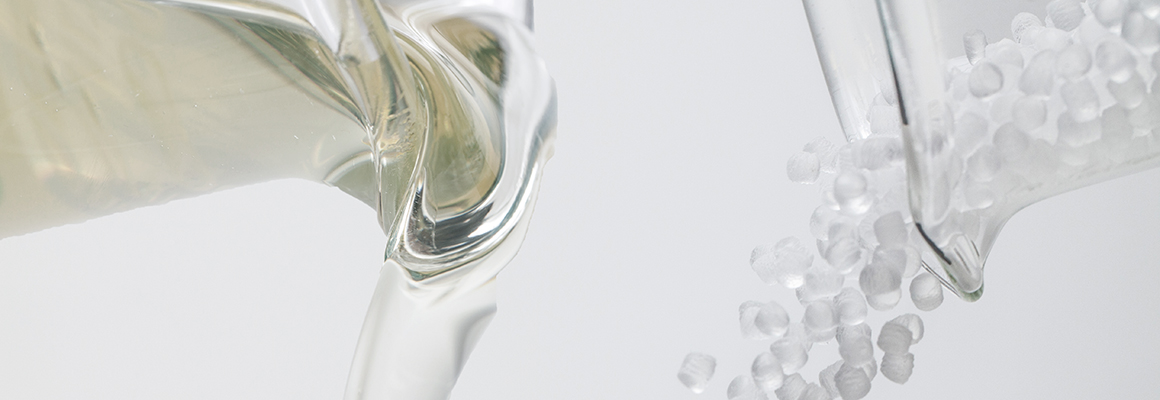
high-performance products
Chevron Oronite is a leading global supplier of viscosity modifiers (VM) under the brand name PARATONE. Our enhanced PARATONE olefin copolymers (OCP) not only provide the benefits of high-ethylene products, such as high thickening efficiency, but also deliver excellent low-temperature properties and the shear-stability needed for today’s demanding specifications. The PARATONE product line is backed by technical experts and polymer scientists committed to supporting customers and developing products for differing and challenging applications.
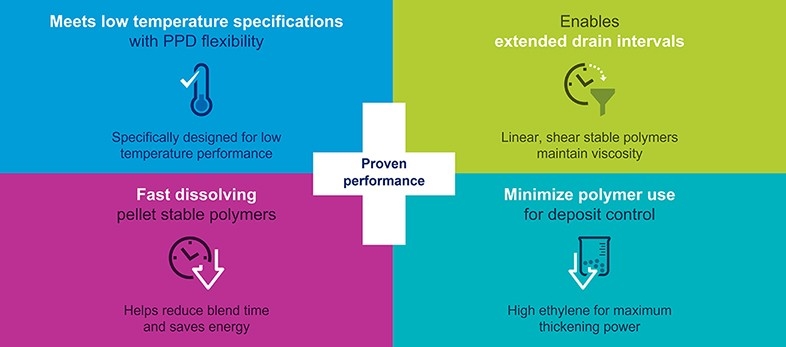
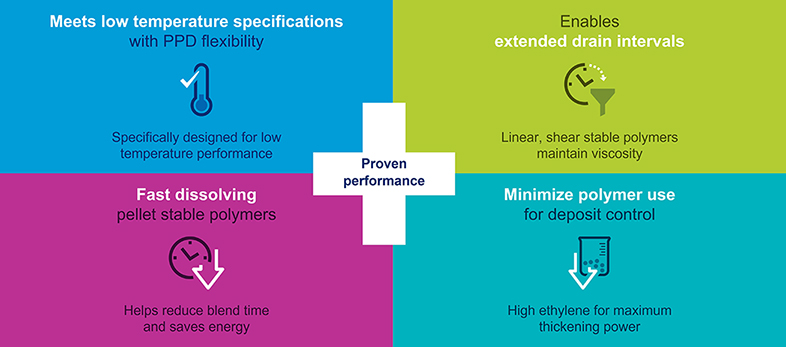
Chevron Oronite can provide the right combination of performance additives and viscosity modifiers to meet a broad range of industry and original equipment manufacturers (OEM) performance specifications at economical treat rates, for passenger car engine oil, heavy-duty engine oil and many other applications.
PARATONE products provide improved formulating flexibility which can reduce the need for costly specialized base stocks in many applications.
a heritage of over 70 years
The PARATONE® brand has a heritage dating back to the 1950s. The first OCP viscosity modifier was created in 1970 and even more innovations since. The PARATONE product portfolio has products available in pre-dissolved liquid concentrate form, or in solid polymer form.
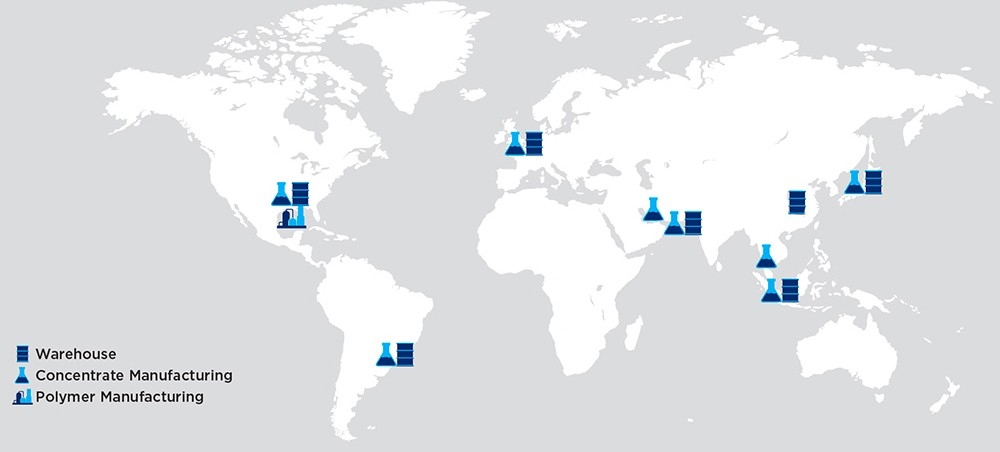
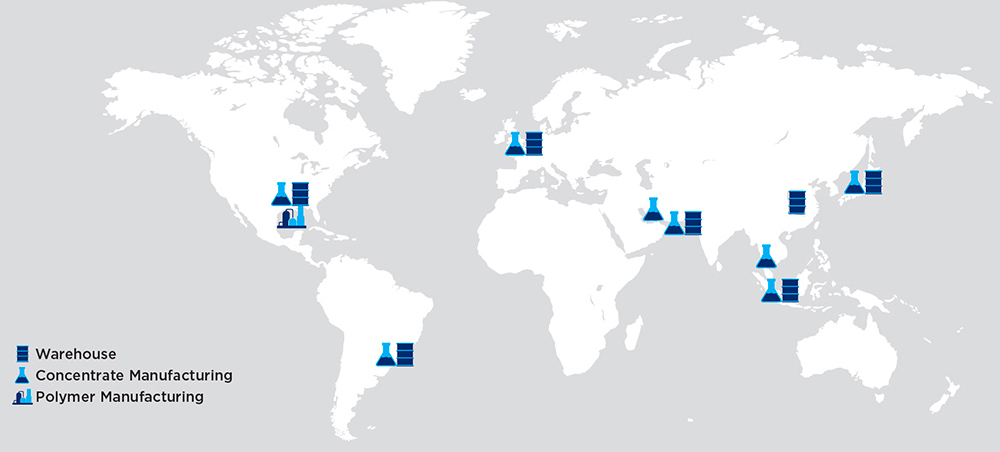
global manufacturing and warehousing
Today, Chevron Oronite manufactures viscosity modifier concentrates in twelve qualified facilities around the globe. We supply polymers from multiple locations to ensure supply reliability and responsive, customer-focused support.
featured products
PARATONE® 8900E is a 24 SSI high ethylene OCP for passenger car and heavy-duty motor oil applications.
PARATONE® 8935E is a 35 SSI high ethylene OCP for passenger car motor oil applications.
PARATONE® 24EX is a liquid concentrate of PARATONE 8900E for group II base oils.
PARATONE® 8004E is a liquid concentrate of PARATONE 8900E for group II base oils and includes a pour point depressant (PPD).
PARATONE® 35EX is a liquid concentrate of PARATONE 8935E for group II base oils.
PARATONE® 8071E is a liquid concentrate of PARATONE 8900E for group III base oils.
PARATONE® 9330 is a high-performance liquid concentrate for group III base oils.